how to used machinery Automatic milking
Automatic milking
The milking machine is designed to pull the milk out of the breast by means of a pump that discharges the air, as in the case of breastfeeding, as the milk flows through the discharge done by the baby calf. In the case of the machine, the discharge is performed.
The continuous discharge causes damage to the nipples so the area around the nipple is isolated from the outside through the rubber envelope and the Teat cup. The pressure and discharge is arranged around the nipples by the so-called pulse.
The importance of using milking machines:
The importance of using milking machines is as follows:
1 - pull the milk from the hernia in the shortest possible time.
2 - Milking milk is free of impurities and pollutants and thus improve the quality of the product.
3 - prevention of the epilepsy from inflammation.
4. Keep animals from transmission.
5. Reduce the cost of milking, especially in large farms.
Automated teller machine
Automated milking systems can be divided into the following types:
1 - the system of milking the vessel or installment
2- Mobile milking units system
3 - system of milking pipes inside the amber
4- Special milking system
5 - Automatic milking system
The first three systems are carried out within the breeding compartment while the other systems are carried out in milking areas outside the breeding ground.
First: Milking systems in the breeding compartment include:
1 - system of milking cup or installment
It is a system in which the discharge unit is installed in a place outside the breeding compartment and the air discharge pipes are installed on the side of the amber with control valves where the milking unit will be connected so that the milking unit is connected by a long hose to the valve in the airflow pipe. Aleppo animals are in place in the amber.

2 - the system of mobile milking
A system in which the vacuum pump and the milking unit are fixed together on a wheeled chassis that is transported between the animals in the amber. Thus, the animals can be milked in the amber without the need to transport them outside the amber and does not need to create a special place for the milking.
This system is divided into three forms:
a. Aleppo mobile unit for two cows at once in two sets of stainless steel capacity of 30 liters per unit with a vacuum pump and motor 220 volts.

B. Mobile milking of two cows at once with one piece of stainless steel The capacity of the 40-liter installment with a vacuum pump and a 220-volt electric motor.
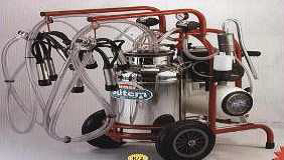
C - Aleppo mobile unit for milking one cow with one piece of stainless steel capacity of 30 liters with a vacuum pump and motor 220 volt.
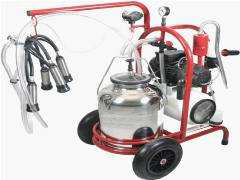
3 - system of milking with pipes inside the amber:
This system is characterized by the following:
Transfer of milk through pipes does not require labor to transport it.
B - does not need to move the cows from their place.
C - does not need to create a private building.
Disadvantages of this system:
1. Costs for establishing larger than previous systems.
2 - needs a large amount of water for the washing process.
3. Pressure in the pipeline shall be reduced as the length increases.
4- The difficulty of calculating the daily production of each cow separately.
5 - Can not see the cups of milk during work because the worker stood on the same level as the cow
6 - height of the level of the pipe from the level of the mast may cause the drop of discharge within the udder.
7 - The system needs to pump high discharge capacity and to a large discharge line.
This system is characterized by the following:
Transfer of milk through pipes does not require labor to transport it.
B - does not need to move the cows from their place.
C - does not need to create a private building.
Disadvantages of this system:
1. Costs for establishing larger than previous systems.
2 - needs a large amount of water for the washing process.
3. Pressure in the pipeline shall be reduced as the length increases.
4- The difficulty of calculating the daily production of each cow separately.
5 - Can not see the cups of milk during work because the worker stood on the same level as the cow
6 - height of the level of the pipe from the level of the mast may cause the drop of discharge within the udder.
7 - The system needs to pump high discharge capacity and to a large discharge line.
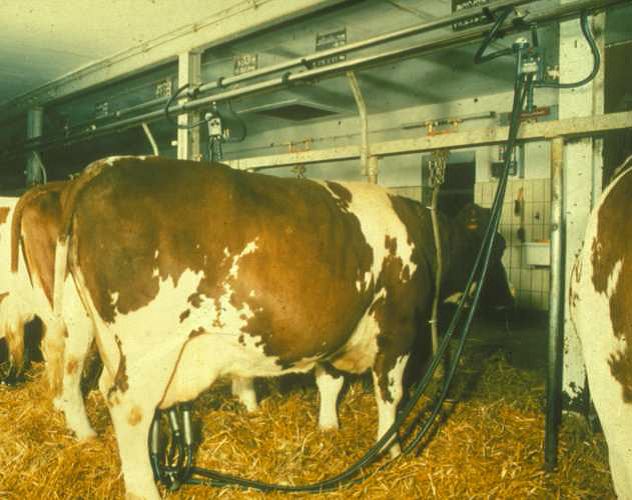
Second: milking machines with special place.
It is a fixed Aleppo system in a place independent of the place of education.
It is characteristic
1 - No need to exert effort in the operation.
2 - gives flexibility in increasing the number of cows that are milking per hour.
3 - does not require any kind of brushes under the animal during the milking process.
4- Shortening the length of the discharge pipes and pulling the milk, which reduces the problems of discharge.
5. One worker can operate the entire system with high efficiency.
It is a drawback:
1 - high structural costs where the milking room is created and the parking lot is created.
2 - Clean the waiting place for cows ready for milking.
3 - slow system of circulation and transport of dairy cattle and dry cows in this system.
It is a fixed Aleppo system in a place independent of the place of education.
It is characteristic
1 - No need to exert effort in the operation.
2 - gives flexibility in increasing the number of cows that are milking per hour.
3 - does not require any kind of brushes under the animal during the milking process.
4- Shortening the length of the discharge pipes and pulling the milk, which reduces the problems of discharge.
5. One worker can operate the entire system with high efficiency.
It is a drawback:
1 - high structural costs where the milking room is created and the parking lot is created.
2 - Clean the waiting place for cows ready for milking.
3 - slow system of circulation and transport of dairy cattle and dry cows in this system.
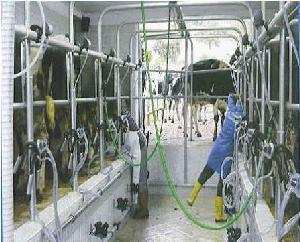
Third: automatic milking system
It is a fixed Aleppo system in a place independent of the place of education. The most special milking operation is done automatically.
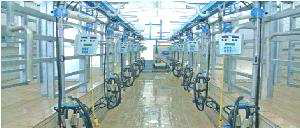
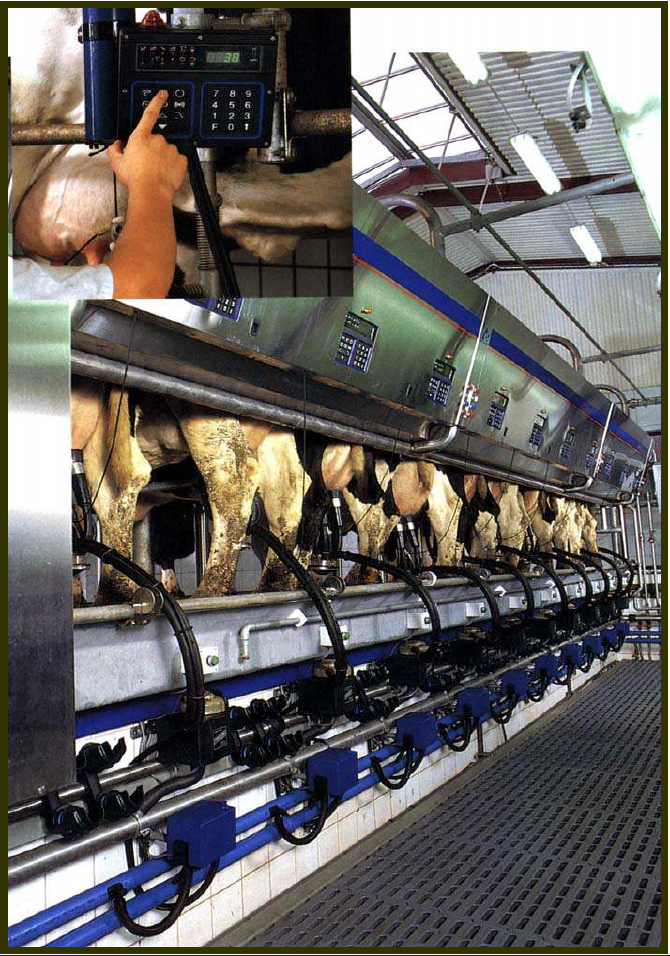
Components of the milking machine
Automated milking machines consist of the following main components:
1- Discharge unit
2. Pulse unit
3- Milk unit
4- Milk transport unit
First: Discharge Unit:
The discharge unit consists of the following:
1 - pump air discharge
2- The barrier or the reservoir
3. The trap
4. Pressure regulator
5. Discharge pressure indicator
6. Discharge pipeline
1 - pump air discharge
The discharge unit pulls the air out of the system to be under vacuum to pull the milk out of the nipples. This is done using the air pump and the pump is selected to accommodate all air volume in the system. The pump capacity is calculated by cubic feet of air / min or cubic meter / min.
Pump performance depends on:
1- Number of units operating in the system.
2. Length of pipes and hoses.
3. Type of system used.
The common type of vacuum pump is the positive displacement rotary pump (8) where a cylindrical body is mounted on which a sliding implant is installed that pulls the air out of the inlet and outputs it from the exit slot under pressure.
The power is transferred to the pump through a hoop mounted on the pump and installed on it that draws movement from the power source.
Several types of power sources are in use:
1- Electric motor.
2- Gasoline engine.
3. Rear tractor shaft.
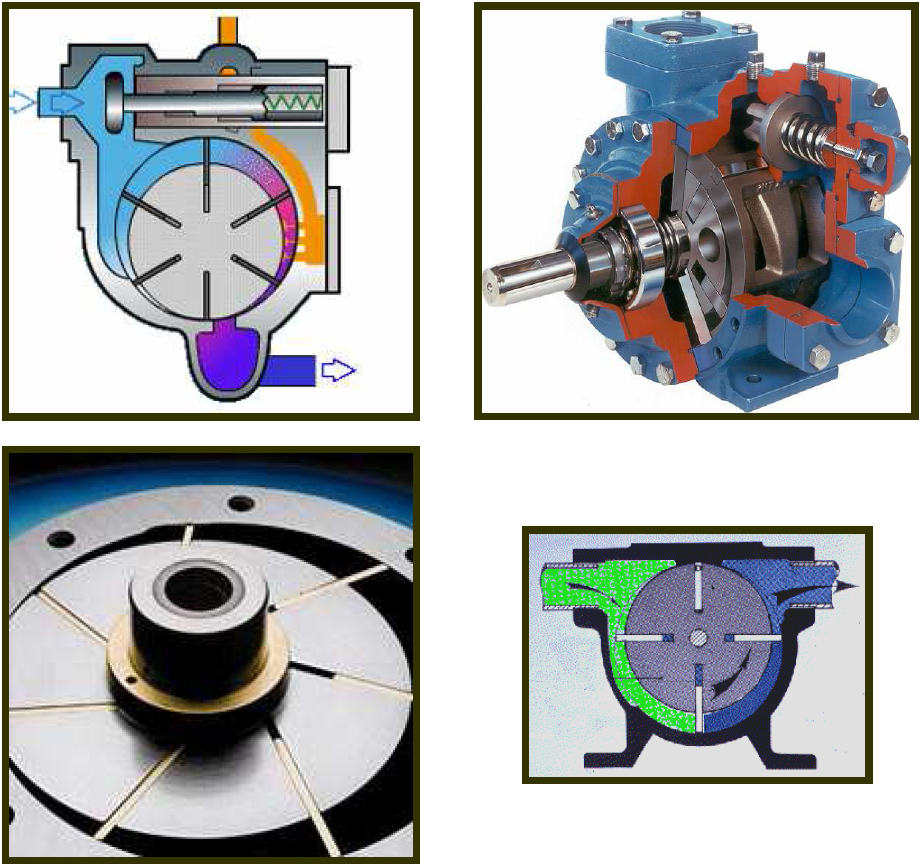
The second part of the discharge unit protects the pump from entering any liquids during the air discharge process and must have a minimum capacity of 15 liter / minute barrier and is in the form of a vessel installed between the pump and the discharge line and also compensates the loss of pressure in case the difference is small and the barrier It has a valve that opens when the pump stops to remove the fluid that collects inside it and must be nearby to facilitate the operation of the jaw and its installation.
3. The trap
The trap is almost the same as the barrier, where the pump is kept from entering the fluid and installed on the line between the milk unit and the vacuum pump, preventing the passage of milk droplets into the pump body. The pipes connect the pipe separately from each other with a separate entrance. Of the worker until it can be dismantled and installed and be self-discharge when filled with liquid to prevent the passage of liquid to the pump and the volume must not be less than 3 liters.
The trap is almost the same as the barrier, where the pump is kept from entering the fluid and installed on the line between the milk unit and the vacuum pump, preventing the passage of milk droplets into the pump body. The pipes connect the pipe separately from each other with a separate entrance. Of the worker until it can be dismantled and installed and be self-discharge when filled with liquid to prevent the passage of liquid to the pump and the volume must not be less than 3 liters.
4. Pressure regulator
The discharge pressure regulator is a valve that opens and closes itself when pressure varies within the system and is installed on the discharge line. The volume of air escaping from the regulator must be within 35 liters / min.
The discharge pressure regulator is a valve that opens and closes itself when pressure varies within the system and is installed on the discharge line. The volume of air escaping from the regulator must be within 35 liters / min.
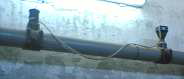
5. Discharge pressure indicator
The discharge indicator indicates the discharge level in the system, which should be 5 t. Air pressure or 50 kPa to indicate the regulator's validity and the validity of the pump and thus correct the defect in a timely manner.
6. Discharge pipeline
The discharge pipe is made of metal or PVC. The pipeline connects the pump with the milking system and is fitted with a regulator, buffer, trap and pulse. The pipe is 25 mm or 32 mm in diameter.
Second: the unit of pulses
The pulse unit is the unit for opening and closing the discharge in the rubber nipples to generate the pulse process from the pressure and discharge to the milking process. The spring takes its movement through the air discharge line of the vacuum pump. The spring is composed of a rubber membrane that moves according to the pressure of the discharge. 50 or 60 pulses / min. The ratio between the milking stage and the rest phase is also determined. The ratio is 40-60. This means that the discharge is done 60 times and the rest is 40 times. This is called. In the case of the large fan, the electric spring is used. There is a main spring. In the springs a
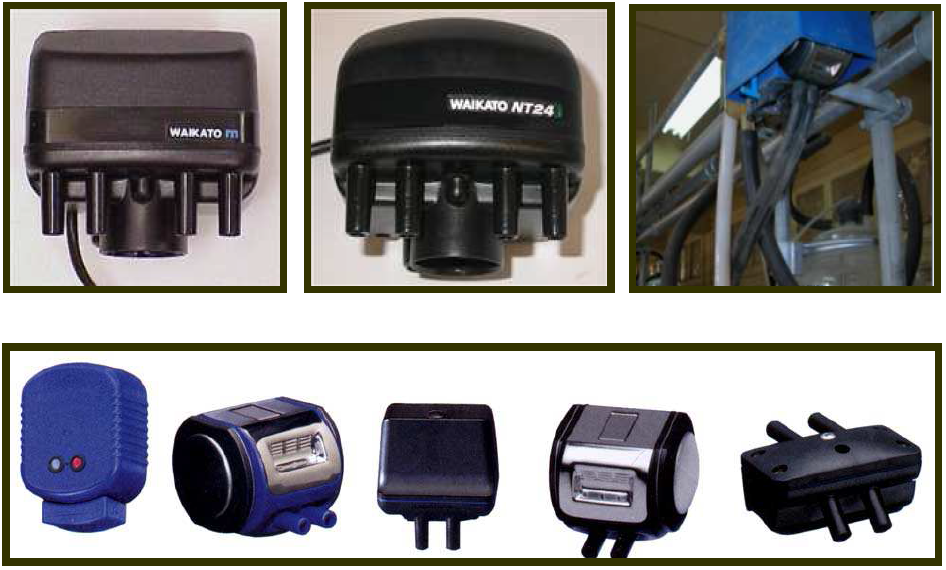
Third: the milking unit
The milking unit consists of milk cups and consists of four nipples and tubes pulling milk and air tubes. All this is gathered in a part called the claw or the coffee complex. The milk transport line, the air line and the spring line are extracted from the claw. The claw shape varies according to the milk system. There is an opening to exit the long milk hose and open it to enter the short milk hose line and the short discharge hose. In the rest of the systems, it contains the pulse tube and the short milk tube from the nipple lines. The long milk line and the long pulse line come out. 50 cm 3 up to 500 cm 3 There is a hole to enter the air
Fourth: Milk transfer unit
The milk is transferred from the conveyor system or vessel through the discharge of the small bowls into a large, 46-liter portable container that is transported to the large pool by the workers.
In the milking system (piping), the milk is transferred through the milk tubes to the large compound on the farm.
In the milking system with the assigned place, the milk is transported under the influence of the unloading to the measuring vessels that measure the production volume of each cow. The milk is then pulled by a valve to the milk receiving unit. The milk is pumped to the large tanks on the farm. Through a buoyant self-movement filled and give a reference to the electric motor, which manages the pump and withdraw milk and this is called receiver unit.
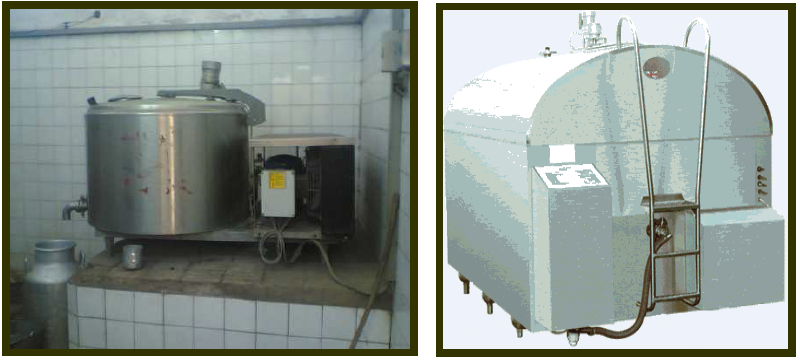
%20اللبن.png)
Forms of automated teller cases
1- Sequential (tandem):
Where the cows stand one behind the other and be stationed in one row or two rows and the distance between the sides 1.3-1.8 m The difference between the ground on which the animals stand and the ground on which the worker stands about 80 cm to allow the worker freedom of movement and control of the milking and The rectangular shape is 2.4 m long and 80 cm wide. It has an entry hole and a side exit slot in the far side of the corridor where the worker stands. This design does not allow more than four couplers behind each other in the same line. The worker can serve these four lanes because the distance between each 2 units 2.4 m.
- Fish Shape:
Is a development of the dual system, but with the difference of the shape of the traditional cleats, where tilted at 30 angles on both sides of the corridor where the worker stands and there is an overlap between cows and this system fits small items and was modified to suit the cows of the Friesian.
3 - the bovine staggered side:
Where the cows stand beside each other in the Almoravet and have food in front of it and there is a track in the back to determine the place of parking and enter the cows from the distance behind the stall where the worker stands for the process of milking, and this system is where the difference between the surface of the ground on which the worker stands and the surface of the ground is about 40 cm.
4- Ring-shaped propeller:
This system can be rotary and milking devices rotary tray and each link serves one unit of Aleppo and this system can 40 studs in a round shape where the cows stand next to each other and face to the circle and the worker stands in the outer perimeter of the circle and at a level of less than 80 cm from the level of China and stands cows in the space to wait before Then enter one after the other according to the places in the Chinese and then with the arrival of the first cow to the end of the circle have been milking the cows out of the pit forward and descend from the tunnel down the Chinese and go out to the exit distance to enter another cow place and this system is large and expensive. There are several forms of circular milking system, including:
A-ring ring system:
It is simpler and cheaper than the previous regime, where cows stand with their hindquarters to the outer perimeter of the mast and the cow comes out with its back at the end of the milking process. The number of couplers ranges between 15-40 knots and each berth serves the Aleppo unit and is operated by one or three workers according to the number of fasteners. The circle at the arrival of the cow end of the cycle and the presence of iron fence behind the cow makes it feel safe and no hesitation when entering the Chinese.
(B) The circular ring system:
The position of the cows is consecutive where the head of the one is in the tail of the other and they are surrounded by a wall of iron and the worker stands in the inner perimeter of the circle and the worker is less than the Chinese level about 80 cm and the length of the link is 2.5 meters and this makes the circle large and there is of this type type several models serve Several couplings range from 5 to 22 and this model is more commercially successful.
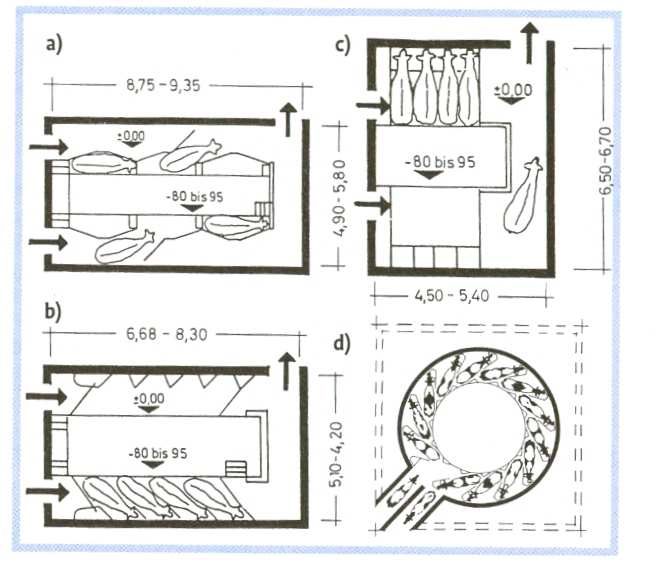
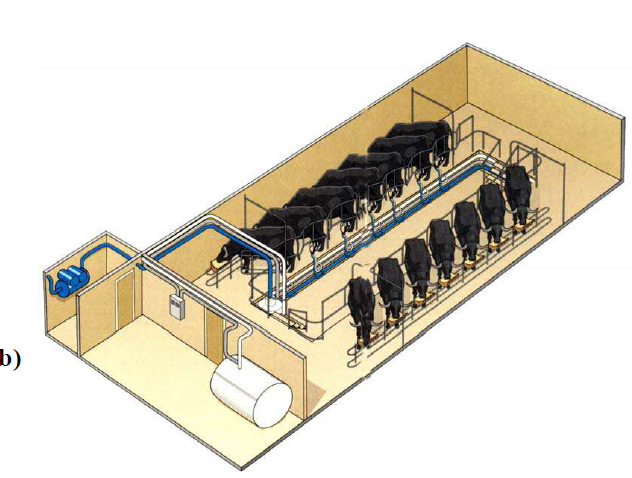
C - system of the shape of the rotor fish:
This system can accommodate more cows where there is overlap between cows and there are different sizes 12-28 and smaller size and 11 bars served by 11 working units and this system milking 100 cows / hour.
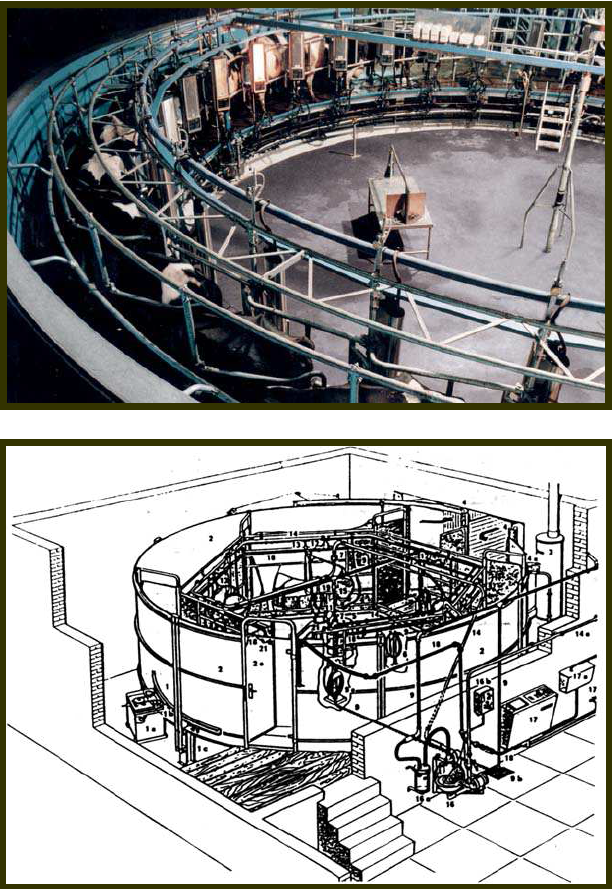
Steps for Automated Milking:
The process of milk milking is one of the most important processes that take place in the farms of animal production, where you need special care in terms of cleanliness and accuracy in the process of milking, whether it is done manually or machine milking machine, so you must follow the following steps to ensure the process of milking efficiently.
Steps of processing the animal before the milking process:
Must be sure to clean the hands of the young man and the cleanliness of animal feed and then follow the following steps:
1 - Wash the nipple and nipples with water in sufficient quantity to remove the dirt, and add disinfectant such as iodine and chlorine with washing water to eliminate the microbes that cause mastitis, and also used iodine and chlorine in the purification of rubber nipples of the milking device before the milking process.
2 - The nipples are washed well to remove the effects of pollution that fall from the nipple on the nipples during the washing process.
3. The nipples are dried with an appropriate towel after washing. It is preferable to use paper tissues so that the infection does not spread from one animal to another.
The use of cloth towels causes infection among animals.
The cleansing and cleaning process takes about 40 seconds and the animal is clean.
4 - withdraw the amount of milk from the nipples before the start of the milking process to determine the validity of the milk and the extent of milk injury microbes to be treated animal and exclusion of milk infected.
The process of processing the animal for milking is about two minutes, and uses a vase to take a sample of each nipple and is called a black surface granular to show any change in the color or form of milk that was taken where in the case of milk with microbes, it occurs in the form of clusters appear clear On the surface of the cup.
If the cleaning process is not complete and the milk is pulled out in good shape, the animal feed is not taut and loose. The nipples do not take milking, either when the processing process is efficient, the udder is full and the nipples filled with milk.
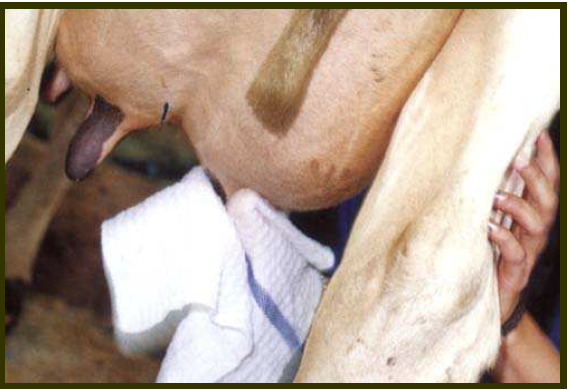
Steps of milking:
1 - Run the milking or milking machine with the correct pressure of discharge by reading the pressure meter and be on 50 kPa (0.5 air pressure).
2 - Detection of any leakage of air from the joints and parts of the canister to eliminate any malfunction caused by low discharge, causing damage to the animal and the fullness of the milking process to the fullest.
3 - The installation of milking units animal feed The milking units are composed of rubber nipples, metal casing and milk compound where the air valve is opened and the rubber nipples are lowered down. The first nipple, which is mounted in the nipple, is then raised to the north and then raised to the right nipple, The front nipple is then north and the front nipple is right. Thus, the milking unit is performed in the udder, which must be within 15 to 30 seconds so that there is no chance of entering the outside air into the nipples that have been installed. The incidence of inflammation
4- Milk is observed from the four quarters through the transparent part of the milk compound or through the milk transfer hose from the milk compound to the milk conveyor tube where it is of the transparent type allowing the milk to be observed.
5 - When low rate of milk production massage the breast from the sides in a circular shape in order to withdraw the remaining milk from the udder to give the opportunity to form a new milk and activate the breast again.
6. After finishing the massage process and stop all nipples once, where the left arm is placed around the set of nipples to be pulled at the fall, and should avoid pressure on the base of rubber nipples so as not to cause the air to enter the nipples that still work, causing mastitis.
C - Steps after the completion of the milking process
After the milking unit is removed, the ureter is disinfected and iodine and chlorine are used to cleanse the nipples by dipping the nipples into a glass filled with feces.
The process of cleaning the milk and washing after milking directly and use an alkaline cleaner, preferably the type recommended by the company producing the pulp and the process of washing in three stages.
1- Wash with lukewarm water and continue for 2 minutes.
2 - Washing with alkali detergent and the rate of 125 g per 40 liters warm water 60 degrees Celsius and this cycle lasts about 15 minutes.
3 - the final rinse with lukewarm water and lasts about 5 minutes to get rid of the remnants of the detergent.
The washing cycle consists of the following parts:
1- Wash basin and have plastic capacity of 80-120 liters.
2 - Automatic control of the washing cycle time and have a plastic container to put the cleaner.
3 - Automatic drainage valve to drain water after the end of the washing cycle.
4- The triangular valve is installed on the water withdrawal pipe from the wash basin.
5- Washing lines.
The laundry hose is divided into two parts: the first feeds the laundry kiosk, from which the water comes out, to clean the milking unit, the second feeds the measuring container and the ratio between the amount of water entering the container and the inside of the laundry plate is controlled by a locker at the entrance of the washing hose. .
How the washing cycle works:
The water basin is filled by running the automatic control panel for the operating time. The basin is filled with water, the triangular valve is placed in the washing mode and the water is drawn in the line of the washing pipes until it reaches the wash hose. The water is divided into two parts:
The first enters the milk measuring container and descends in the form of a water stream on the wall of the vessel through the water distribution zippers.
And the other part goes to the laundry kiosk and comes out in the form of a fountain to wash the nipples and then go to the milk complex and then to the milk and then to the milk measuring container and then descend to the milk transfer hose to the line of milk delivery pipes and then to the final reception unit, which push the washing water to the wash basin one more time.
This process continues until the specified period of time has elapsed. The automatic drainage valve discharges the water and re-fills the basin with water again for a new cycle to rinse with clean water. After the wash cycle, the triple valve is returned to the milking position to be ready for milking again.
No comments